Materials
A wide range of ceramic oxide materials can be used for crucibles, the type being dependent on the metal/alloy, the basicity of the melt and the foundry practice, whether erosion resistance or thermal shock resistance takes prominence.
The most common type, historically, are the aluminosilicate range; these were based on clays but now utilise the purer synthetic materials. At one end of the range lies fused silica, with an excellent thermal shock resistance, whilst at the other extreme is fused alumina with a very good erosion resistance.
Magnesia generally offers better chemical and erosion resistance, but is better suited to the faster cycling times. The most resistant material is zirconia, and there are many iterations of this to suit different applications.
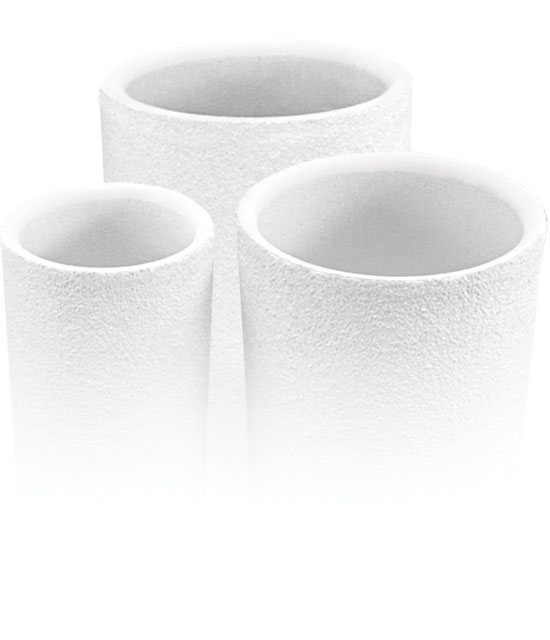